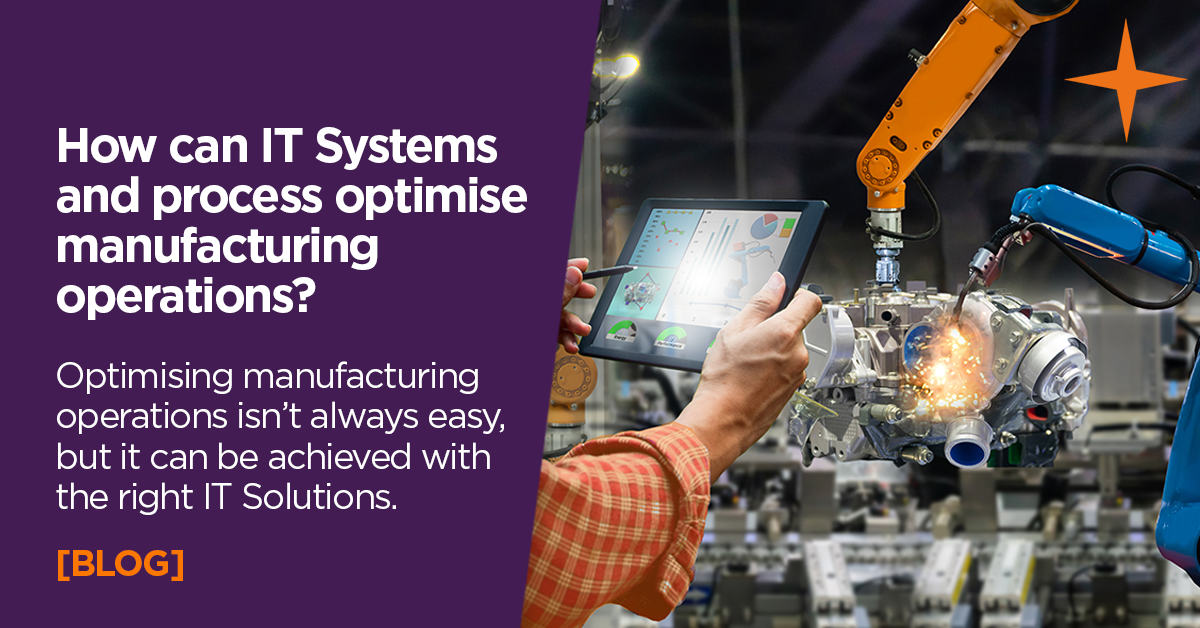
Optimising manufacturing operations isn’t always easy, but it can be achieved with the right IT Solutions.
Manufacturing businesses are typically the best at seeking out efficiency and productivity in their operations, particularly on the shop-floor. However, many still do not apply the same LEAN principles to the rest of their operations, and that can mean the optimisation of processes is more challenging because of a lack of consistency throughout the business.
Systems and process analysis, and automation can be used throughout an organisation to drive down inefficiencies. IT is certainly an enabler of an efficient and well-performing optimisation.
As QuoStar’s Robert Rutherford was recently quoted in the Manufacturer: “Finance operations, for example, are often very bloated, but IT can facilitate outsourcing or offshoring, not only reducing costs but also allowing the process to become quickly automated to a good extent.”
What types of IT solutions and services can help with Optimising manufacturing operations?
Historically, manufacturers were always at the forefront of technology. This has in many ways meant that they experienced the falls and disappointments that come with testing cutting edge solutions. However, technology systems have also been driving results for manufacturers in some areas – such as IoT, cloud services and CRM.
Internet of Things (IoT)
The Internet of Things (IoT) has certainly given advantage to manufacturers both on the shop-floor and within their products on customer sites – by helping in support and maintenance, but also in querying big data for insights and value. It’s driving decisions around productivity, wastage and research & development to deliver wins across the board.
Cloud Services
Cloud services are also still extremely valuable to manufacturers. Although many still keep heavy processing in a private cloud, the public cloud (particularly AWS and Azure) allows operations and development to flex, trial and scale-up (and scale-out) without the traditional costs and complexities of big kit in the server room. The pandemic has heavily accelerated change. Customers have demanded faster innovation, more data and information, greater integration, and increased security.
CRMs
CRM systems have moved on significantly and its greatly improving the service manufacturers are able to deliver to customers, whether it is on managing expectations, delivering value or collecting relevant information. They can also drive an increase in sales in terms of new business wins, cross-sales and real-engagement with marketing automation.
Big CRM projects were historically associated with large capex costs. However, now they virtually all come in a cloud-based delivery model on a price per user basis.
Digital Transformation Road Mapping & IT Consultancy
QuoStar specialise in IT solutions. We can help with Digital Transformation Road mapping, as well as offering IT Consultancy services. Don’t with QuoStar you also have access to a CIO Service too!